
The logging procedure certified by IBAMA
Our suppliers are located in the Belem area, in the state of Pará in Brazil.
They all are all legally permitted to cut the trunks of the most popular wood species. Those permits are granted by IBAMA (the Brazilian Institute of the Environment and Renewable Natural Resources) which authorises legal logging to prevent uncontrolled deforestation of the Amazon rainforest and the natural regeneration of the logged plants.
They all are all legally permitted to cut the trunks of the most popular wood species. Those permits are granted by IBAMA (the Brazilian Institute of the Environment and Renewable Natural Resources) which authorises legal logging to prevent uncontrolled deforestation of the Amazon rainforest and the natural regeneration of the logged plants.
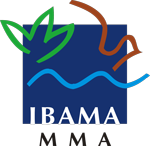
THE WOOD SPECIES WE TRADE
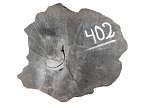
IpeTabebuia
(Brazilian Walnut)
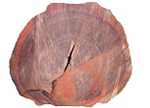
Massaranduba
(Bulletwood)
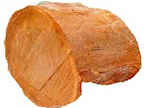
Sucupira
(Brazilian Chestnut)
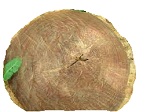
Cumaru
(Brazilian Teak)
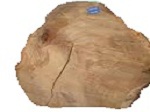
Garapa
(Brazilian Ash)
The Trans-Amazonian Highway
Since the 70s, the Brazilian government has been trying to channel the transport of logs by road through the Trans-Amazonian Highway (5,000 km), but, according to estimates, only 20% of it is currently paved.
The forest, heavy rainfall and uneven geological surfaces severely limit this transport route, which is still unsuitable for transporting wood from the logging area to the sawmills.
The forest, heavy rainfall and uneven geological surfaces severely limit this transport route, which is still unsuitable for transporting wood from the logging area to the sawmills.
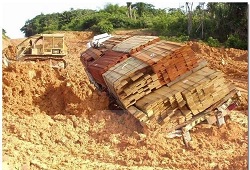
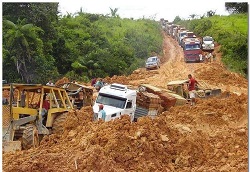
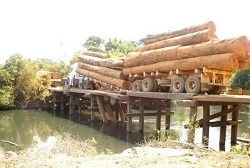
THE JOURNEY OF LOGS ON THE AMAZON RIVER
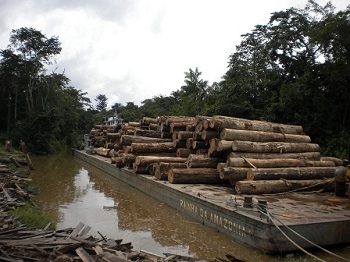

Once cut, logs are loaded onto barges, which are still the best method of transport today.
The journey takes about ten days from the Santarem area to Belem, at the mouth of the Amazon River. The barges have a capacity of between 1,200 and 1,500 m³ each and are pushed by tug boats to the docks of the respective sawmills.
The journey takes about ten days from the Santarem area to Belem, at the mouth of the Amazon River. The barges have a capacity of between 1,200 and 1,500 m³ each and are pushed by tug boats to the docks of the respective sawmills.
CUTTING THE LOGS
Logs are cut into boards of approx. 26 mm, ideal for the production of decking with a 20-mm thickness.
Lengths vary from a minimum of 900 mm to a maximum of 6000 mm.
Lengths vary from a minimum of 900 mm to a maximum of 6000 mm.
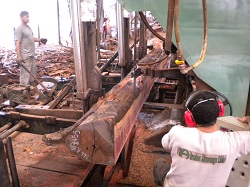
The so-called ‘milk tears’ are a typical feature of the Massaranduba cut.
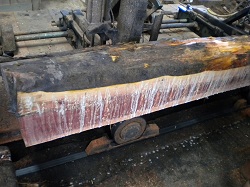
AIR DRYING
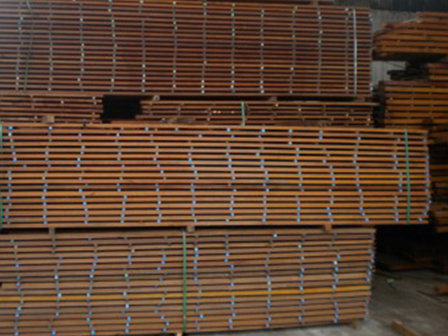
Ipe, which is a rather stable wood, has a great capacity to discharge internal moisture by itself, and once logged, it is left to dry in the open air.
If this procedure is not enough, the wood can be put into drying kilns to reach the required moisture level, which is normally around 16% (±2).
If this procedure is not enough, the wood can be put into drying kilns to reach the required moisture level, which is normally around 16% (±2).
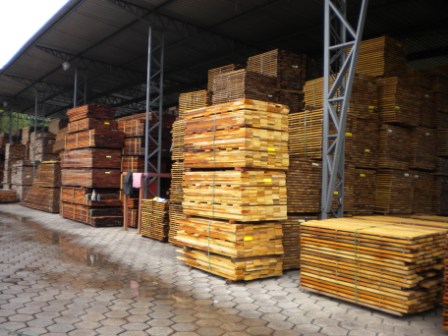
Wood stability is a key factor for a successful decking installation, so drying the timber is an essential step.
KILN DRYING
Other less stable woods such as Massaranduba or Sucupira require drying kilns to expel their moisture.
Each kiln contains about 80 m³ of raw timber and through a process of water vaporisation (to open the pores of the wood) and hot air circulation over a 30-day period, the timber is ready for processing.
Each kiln contains about 80 m³ of raw timber and through a process of water vaporisation (to open the pores of the wood) and hot air circulation over a 30-day period, the timber is ready for processing.
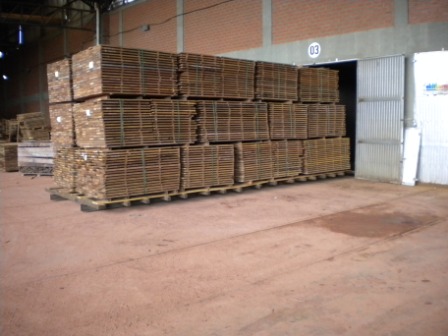
Dried timber is often covered with cellophane to maintain a constant level of moisture.
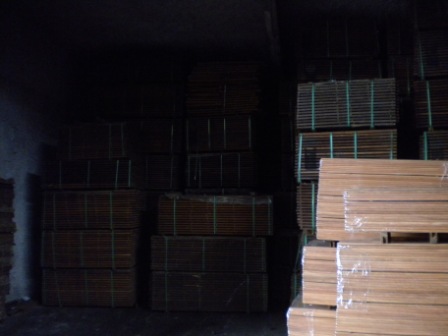
THE ‘ROUGHING’ PROCESS
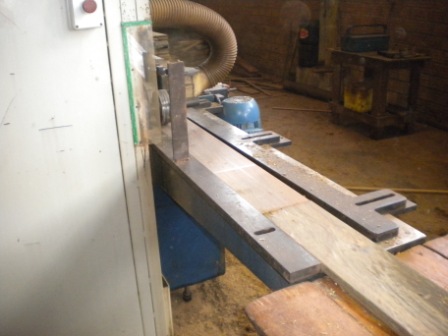
Boards made of raw material need to be roughly trimmed by a planer machine which uses two knives, one at the top and one at the bottom, to remove impurities in a rather rough manner.
This step is important because it allows the next planers, which will definitively shape the profile of the deck, to carry out a precise and burr-free operation.
This step is important because it allows the next planers, which will definitively shape the profile of the deck, to carry out a precise and burr-free operation.
PLANING
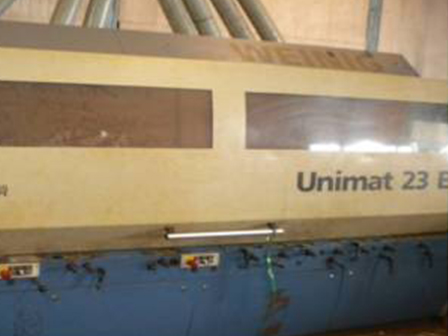
Planers have the most important task in the making of the deck.
The more knives they have, the better the marks they leave on the boards, as well as being able to make several ‘cuts’ on the same board at the same time, S4S, T&G, G&G, EM.
They also make, when requested, dozens of different profiles for making non-slip or ribbed deck boards.
The more knives they have, the better the marks they leave on the boards, as well as being able to make several ‘cuts’ on the same board at the same time, S4S, T&G, G&G, EM.
They also make, when requested, dozens of different profiles for making non-slip or ribbed deck boards.
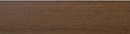
S4S
Surfaced four Side
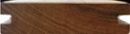
G&G
Groove & Groove
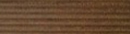
Ribbed
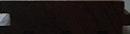
T&G
Tongue & Groove
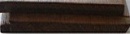
EM
End Matched
PACKAGING
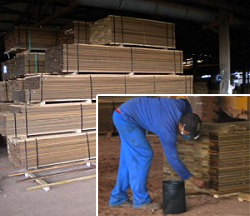
Once planed and cut to the required lengths, the deck is packed.
Once packing is complete, a paraffin wax is applied to the heads of the boards, which prevents moisture (especially when the timber is inside a container with temperatures exceeding 40 degrees) from penetrating into the boards, keeping it constant at around 16% (±2).
Once packing is complete, a paraffin wax is applied to the heads of the boards, which prevents moisture (especially when the timber is inside a container with temperatures exceeding 40 degrees) from penetrating into the boards, keeping it constant at around 16% (±2).
WAREHOUSING AND SHIPPING
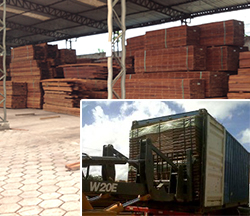
The deck is then ready to be stored and shipped by truck to the Brazilian domestic market and by container to the rest of the world.
From the port of Belem decks are shipped to Europe, while the port of Vila do Conde serves the rest of the world.
From the port of Belem decks are shipped to Europe, while the port of Vila do Conde serves the rest of the world.